The waste management industry is at a crossroads. The regulatory roadmap reveals a challenging future, one in which restricted offshoring of hazardous or otherwise problematic materials means bringing more and more complex processing close to home.
Sir James Bevan, Chief Executive of the UK’s Environment Agency, has suggested that the UK “processes all our waste at home and ends all waste exports as soon as possible”; MEPs have voted to restrict or completely prohibit many forms of waste export with further restrictions likely to follow.
All this while waste itself increases and becomes more complex. Rising consumption of rare earth metals, an increasing appetite for plastic recycling, and a public attitude towards waste which is not yet fully cognisant of its true impact will only cause the challenges to industry to rise exponentially.
Concerns over the environmental impact of mining, the impact of geopolitics on exports, and rising prices of raw materials are all likely to contribute to an increase in the rarity of materials – to the point where the role of waste management will become critical to maintaining supplies. This extends beyond new waste, as landfill mining offers an opportunity both to remove hazardous substances from the earth, and to recover significant amounts of valuable materials lost in decades past.
All of this adds up to significant change – and a significant challenge – in the future of waste management. But it also presents a huge opportunity to the company that’s ready to meet it.
New X-ray sensor technology for a more regulated industry
Many western facilities are not ready. Lines which process domestic waste may do their job well by today’s standards, but separating key materials in this relatively new vertical is more difficult than, say, splitting ferrous and non-ferrous material, or employing machine vision and sensors to tell broad categories of recyclables apart. The next generation of waste management needs those abilities, of course, but it also demands new technology with far more powerful detection capabilities. To handle tomorrow’s waste is to literally see the unseen.
X-rays can do just that. Building a scanner based around Sens-Tech’s LINX linear X-ray sensor detectors allows for fast and accurate detection of specific materials which the smartest machine vision cameras and AI algorithms simply cannot recognise. An X-ray scanner covers a broad sub-UV area of the electromagnetic spectrum and, properly adjusted for your needs, can identify critical materials by seeking out evidence of their individual atomic densities through the amount the X-ray energy is absorbed by application specific scintillator materials.
This could help, for instance, with quickly separating different types of plastics, discovering rare materials hidden within electronics, or picking out volatile elements like lithium to ensure their efficient recovery and the safety of processing lines. Such a scanner could also detect the difference between particle board, chipboard and wood, and reliably scan for contaminants in sensitive processes. It could also be designed into brand new waste sorting machines or integrated into existing sorting machine family designs to complement the portfolio of eddy current, sensor and machine vision systems to add brand new capabilities.
The combination of XDAS, the industry’s most comprehensive range of single and dual-energy detection electronics, and LINX, the most flexible and expandable range of X-ray detection cameras, provides next-level sorting. The modular sensor array can be expanded in 100mm modules up to 5m to meet the width of any line and the signal processing electronics can easily be expanded to match the speed of the fastest sorting lines.
Whether you want to integrate XDAS into your own detector housing or you would like a black box solution from us, Sens-Tech is ready to help you meet your sorting requirements, whatever they may be.
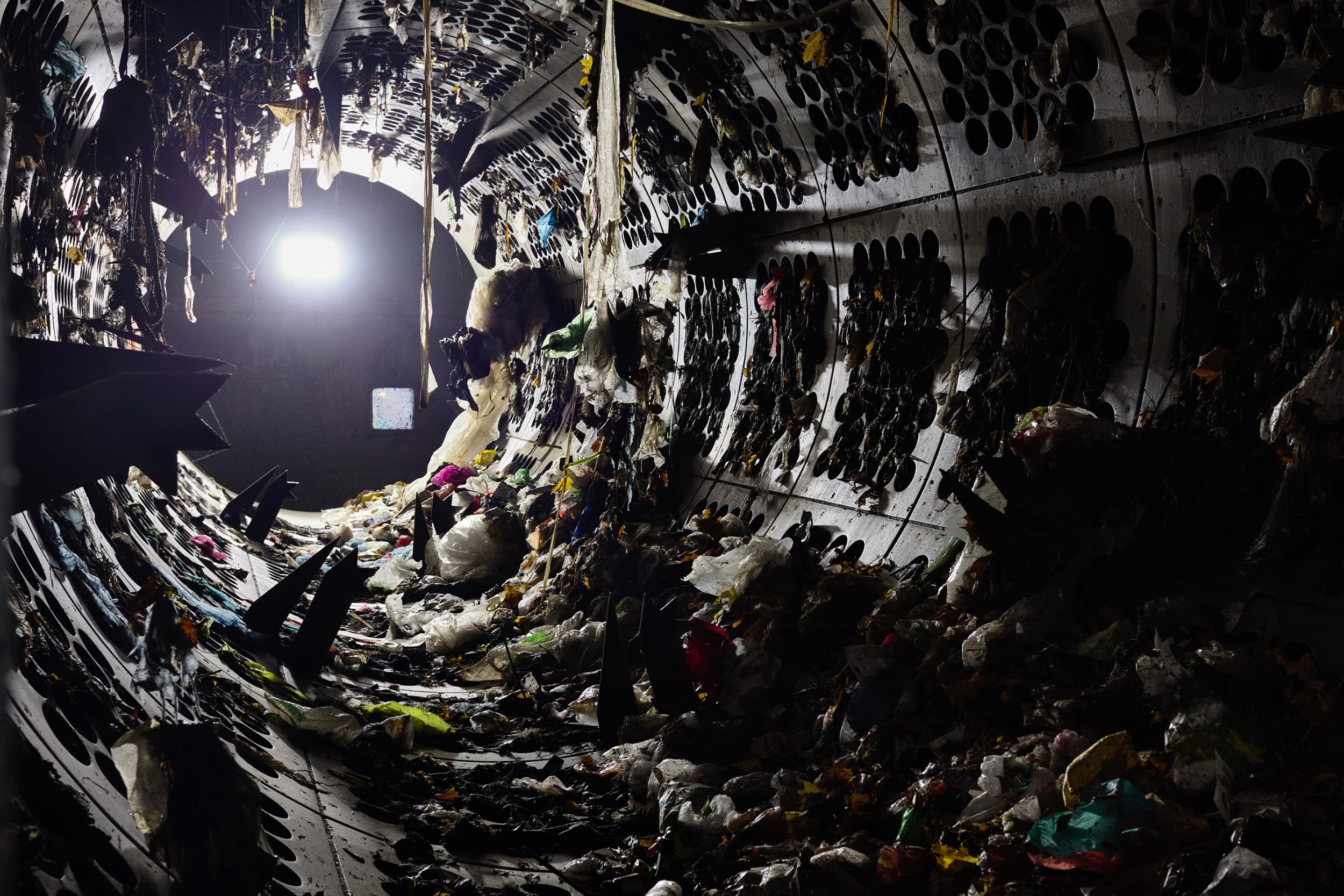
Increasing productivity through reduced downtime
We know that creating machinery for waste management is not simply a case of installing it and walking away. Regular servicing is a vital step to ensure the ongoing accuracy of line sensors. It can also be a cause of major disruption and financial loss; an inactive line is one which isn’t earning, and one which is likely causing significant knock-on effects to other areas of the business. Change needs to come not only in terms of what waste management facilities can handle, but also in the way they ensure they can handle it.
Sens-Tech is aware of the impact that maintenance can have, and the key ways in which that impact can be mitigated. Through regular communication with our customers we have developed, for example, consolidated boards which combine four detector modules into a single easy-to-switch unit to ease the burden on engineers and help minimise downtime.
We also recognise the need to continually maintain hardware through its entire lifecycle. It would be unthinkable to be forced to refactor an entire line because, say, one critical microchip is no longer available from its semiconductor manufacturer. At Sens-Tech we maintain close partnerships with our customers, a keen awareness of the products they rely upon, and a deep understanding of the electronics within. This means that if a vital part changes or becomes unavailable, we can quickly redesign our modules to maintain the same precise performance standards, creating drop-in replacements with no downstream disruption.
Act fast, act smart
It’s important to be nimble. One governmental edict could be all it takes to throw one’s business into chaos because developing, ratifying, and testing brand new equipment to meet new recycling demands could take five or more years. Those that can’t keep up will be left well behind the curve. In a growing industry filled with new contenders and fresh ideas which are redefining that curve every day, that’s not a good place to be. But it doesn’t have to be that way. Quality off-the shelf modular components reduce the burden on creating new equipment; why redesign the wheel?
At Sens-Tech we’re proud of our agility, and our ability to quickly meet customer needs by employing fully tested existing platforms or modifying them to create bespoke solutions. We keep a catalogue of UK-manufactured stock on hand to cut lead times, and we’re ready to support the individual needs of our customers from inception to deployment and beyond.
A business ready for the future of waste management
Even if the deadline to re-shore difficult materials happens to be some way away, or the need to expand or refactor your lines does not yet feel critical, now is the time to act. It’s clear that advanced X-ray sensor technology will be a requirement for the lines of the future, and such technology exists today.
If you choose to build around modular hardware, the core of tomorrow’s scanners is ready to go. The tech doesn’t have to be difficult to integrate, and, based on proven and evolving platforms like Sens-Tech’s LINX, it offers far more than just a drop-in solution. It’s about having the agility to deploy or pivot fast, the backing to do so with expert personalised support propping up your business, and the assurance that the lifecycle of your new installation will be taken care of. The roadmap might be difficult to navigate, but it’s perfectly possible to steer around the roadblocks.
For more information, contact
Paul Hurtado, Head of Sales and Marketing at Sens-Tech.